Spirits manufacturers constantly face many different challenges in their industry, some of the most important being, accelerate proofing, consistent product quality, reduced product giveaway, maximize yields, and satisfying government regulations regarding taxation on %Alcohol by volume. With the JCS UltraBlend™, distillers can meet these challenges by streamlining their production, eliminating the need for Proof Tanks, currently used to obtain the required %ABV (%Alcohol by Volume), Tightening Quality Control(can include added sugar, flavorings, spices, etc.). Ultimately the producer can save in many ways:
Reducing the cost of production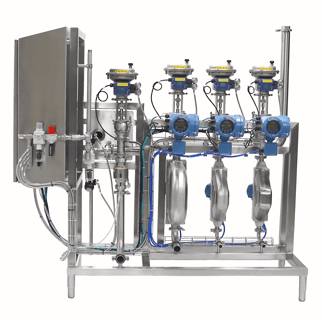
-
- In time
- Costly component giveaway
- Taxation
- Storing of tailings
- Manpower
- Reduced equipment sizes to match bottling rates
- Reducing the need for tailing storage
- Reducing the need for proof tanks
- Reduced horsepower motor sizing
- More product in less time
- Optimized production
- Just producing what is needed
- Smaller equipment
- Reduced tank sizing
Challenges in the industry
In the ever-changing landscape of spirits manufacturing the modern-day leader is faced with increasing demands, reduced timelines, and a shrinking workforce. With bourbon demand on a growth trajectory like never before, producers have been expanding exponentially to keep up with it. However, with each retirement, there’s less and less availability of experts at the helm ready to transition into the next vacancy. Changing the paradigm from Batch to standardization requires embracing new technology, and accuracy that transcends today's measuring instrumentation. The JCS UltraBlend™ with advanced algorithms provides exactly what is needed, it is proven, and acceptable to TTB.
Another quite familiar challenge that many distillery leaders are embracing is that with traditional batching it takes a lot of time to blend the ingredients, proof the ABV, meet yield targets, and all of that requires a lot of floor space to accommodate the process.
To adapt to these challenges in the spirits processing industry, many facilities are beginning to think differently. If we have increasing demand and a decreasing workforce coupled with expansions that are nearing the constraints within the available space, we must think differently about our ways to blend spirits, right? Let us show you how the JCS UltraBlend™ can be the solution to this changing paradigm.
Opportunities to meet the challenges: How the JCS UltraBlend™ can help you
At JCS, we saw a great opportunity within the spirits industry to collaborate and apply the JCS long-standing proprietary engineered algorithms and help resolve some of the current constraints that the Alcohol Beverage industry face.
With traditional alcohol beverage production, most of the industry currently uses; Batch, Batch Continuous, or Ratio Blending into a Proof Tank, where products must be QC adjusted. This has always been required, as, before the JCS UltraBlend™™, there was no accurate way to guarantee +-0.03%ABV or better.
The JCS UltraBlend™ offers a standardization by sub-component (alcohol, sugars, calories, flavorings, and more), whereas the other options available in the market provide a ratio standardization, batch standardization, or continuous batch standardization.
What’s the difference?
Batch standardization as the name implies means mixing ingredients in a tank, Lab QC Testing (Proofing), and then adjusting in small steps to get within the allowable range. In ratio standardization, as the name suggests, each ingredient demand is simply a ratio of the total flow rate based on flow-through meters, and thus cannot be more accurate than the meters, typically 0.25%. For example, if you have the recipe “XYZ” You will add 35% of ingredient X’s flow rate, and 65% of ingredient Y’s flow rate, for you 100% total flow rate. Therefore, since %ABV is not a ratio of flow rates, but rather a measurement of % by finished volume, the straight ratio blending will never eliminate a proof tank, or the Lab Testing and QC adjusting of the finished product, which gets much more difficult when sugar and or other flavors are part of the formulation.
To guarantee that your product recipe is the same every time, if an ingredient falls behind during the production process, the JCS UltraBlend™ will automatically adjust to make sure that the final product has the perfect formulation in every bottle of your line. Furthermore, with the JCS UltraBlend™, you can blend only when and as much as you need, minimizing product losses due to shrink or costly work in process and eliminate the need for tailing tanks or storage. The increased accuracy provided by the JCS UltraBlend™ leads to cost savings of your high-value ingredients to achieve the same results.
Another great attribute for spirits producers is that the JCS UltraBlend™ only takes a single operator to manage the entire system and produces the exact amount of in-spec product you require without correction. Whether the flow is in fractions or hundreds of gallons per minute, the JCS UltraBlend™ delivers your products in precision formulation on demand.
Continuous Benefits of the JCS UltraBlend™
- The system can standardize for multiple constituents simultaneously like %ABV, °Brix, flavors, calories, acidity, salts, and others.
- The standard system capacity goes from 2 streams up to 16 streams and can be custom expanded to as many streams as required. Product flow rates can range from fractional gallons per minute (GPM) up to greater than 600 GPM on each stream of the JCS UltraBlend™.
- Preventive alarm stops the blender before it puts bad product downstream to ensure that every bottle downstream is accurately on formula and eliminate rework or production holds.
- Built-in system diagnostics aid in troubleshooting problems, such as plugging filters, pumping failures, equipment failures, and more, without producing off-spec product in the interim.
- Built-in ingredient database, recipe database, and production reports.
- Ease integration into existing PLCs and or Operational Control Systems.
At JCS our processing systems are built with a maximum of flexibility, and customization, accommodating many changing parameters, to perfectly fit your specific processing needs. Together JCS will partner with you to form a winning team to implement the most value-added, and sustainable solutions to ensure long term success and profitability for your organization.
You supply the ingredients and the JCS UltraBlend™ will deliver perfect formulation time after time, with a fast ROI.